Oxide fibres for Ceramic Matrix Composites (CMCs) have been a key part in advancing materials science, particularly for applications requiring high temperature stability and oxidation resistance. These fibres are integral in reinforcing ceramic matrices, enhancing mechanical properties, and expanding the usability of composites under extreme environmental conditions. The development of oxide fibres began in the 1970s as researchers sought materials that could exceed the performance limitations of metals and non-oxide ceramics in high temperature environments. Initial efforts focused on alumina and silica-based fibres due to their inherent stability in oxidative atmospheres and capability to withstand high temperatures without significant degradation.
One significant milestone in this field was the development of Nextel™ fibres by 3M, introduced in the late 1980s. These fibres, composed of alumina, silica, and boria (Al2O3-SiO2-B2O3), marked a significant advancement due to their enhanced thermal stability and mechanical strength. Nextel™ fibres have since been widely adopted in various high temperature applications, from aerospace to defence, for their ability to maintain integrity under thermal stresses whilst resisting corrosive environments. The 1990s brought further innovations with the introduction of stoichiometric mullite in alumina fibres (3Al2O3 2SiO2). These fibres offered improved toughness and thermal shock resistance over pure alumina fibres, making them more suitable for the dynamic thermal environments that products experience in aerospace and land-based energy applications. This period also saw significant advancements in the processing techniques of oxide fibres, notably through sol-gel and dry spinning methods, which improved the uniformity and quality of the fibres.
In the early 2000s, the focus shifted towards optimising the cost-effectiveness and engineering flexibility of oxide fibres. The adoption of fibres with higher denier and modifications in fibre chemistry to include rare earth elements exemplified efforts to enhance performance characteristics such as creep resistance and thermal stability. These enhancements have broadened the applicability of oxide CMCs, pushing them towards more mainstream adoption in various industrial sectors. Recent developments have concentrated on refining the properties of oxide fibres to meet the specific demands of advanced applications. Innovations in fibre architecture and composite processing techniques have enabled the development of CMCs that can perform under greater thermal and mechanical loads. The ongoing research aims to further reduce costs and improve the performance of oxide CMCs, ensuring their competitive advantage over traditional materials such as titanium and other high-temperature alloys.
Available Fibres
This section delves into the three predominant fibre types typically used for CMCs —oxide fibres, carbon fibres, and silicon carbide (SiC) fibres — each offering unique properties that cater to specific demands and requirements.
1. Oxide Fibres
As discussed, oxide fibres, such as alumina and mullite, are renowned for their high temperature stability, making them ideal for challenging thermal environments. They exhibit excellent resistance to oxidation, crucial for applications that are exposed to an oxygen-rich atmospheres at elevated temperatures. Additionally, these fibres are generally less expensive compared to other high performance fibres like SiC, providing a more cost-effective solution for various applications. However, they typically have lower strength and stiffness and are susceptible to creep under high temperature stress, which may limit their use in load-bearing applications.
Specific types of oxide fibres include Nextel 610 from 3M, which is favoured for its high alumina content and suitability for high-temperature applications due to excellent resistance to thermal shock and oxidation. Nextel 720 offers lower strength but higher thermal stability, ideal for higher temperature environments, while Nextel 312 and 440 offer a range of properties tailored to specific needs from automotive to aerospace, where cost and thermal performance are pivotal.
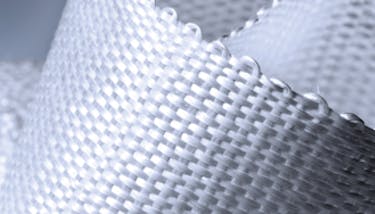
Hiltex's development in continuous alumina-silica fibres stands out through its utilisation of dry spinning technology, paired with an extensive background in fibrous refractory manufacturing. The resulting HILTEX ALF fibres are comprised solely of alumina (Al2O3) and silica (SiO2), making them stable oxide fibres. These fibres are notable for their fine filament diameter (7-10 microns), which enhances their flexibility and strength, characteristics often compromised in other high performance fibres due to the inclusion of materials like boron. ALF fibres exhibit excellent chemical resistance, thermal shock resistance, and electrical insulation properties. They are available in various alumina-silica ratios, with the highest grade fibres resistant to temperatures up to 1395°C. The cost of oxide fibres typically ranges from $50 to $250 per kilogram.
2. Carbon Fibers
Carbon fibres are known for their excellent tensile strength and stiffness, making them indispensable in structural applications requiring lightweight composite materials. They can withstand very high temperatures, over 2000°C in inert environments, making them suitable for space and specialist military applications. Despite their advantages, carbon fibres rapidly lose strength in oxidising atmospheres above 500°C, which significantly limits their applications for high temperature composite materials. Polyacrylonitrile (PAN) based fibres like Toray’s T300 are widely used in aerospace and automotive sectors for their strength, while pitch-based fibres are chosen for applications that require exceptional rigidity and thermal conductivity. Carbon fibres typically range from $20 to over $500 per kg, depending on the fibre’s modulus and intended application.
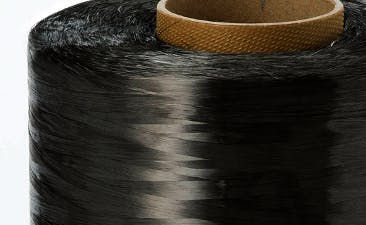
3. Silicon Carbide Fibers
SiC fibres are exceptional in preserving their strength and stiffness at temperatures that surpass the limits of both oxide and carbon fibres. These fibres offer excellent resistance to chemical attack and oxidation, making them suitable for use in harsh environments at over 1300°C. They provide a good balance of mechanical properties, including high strength, stiffness, and thermal conductivity, making them favoured for advanced applications in defence and aerospace. However, the complex production process for SiC fibres makes them one of the most expensive fibre types available, limiting their use to high-value applications. Like many ceramic materials, SiC fibres can be brittle, which may limit their use in applications requiring high impact resistance. SiC fibres are generally priced from $200 to over $1000 per kilogram, reflecting their superior properties and the complexities of their production process.
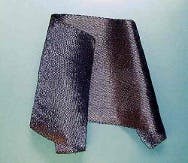
Developments
The development of new ceramic fibres plays a pivotal role in defining the capabilities and applications of CMCs. This section explores the recent advancements in oxide fibres introduced by three significant players in the market: RATH Group, Saint-Gobain Advanced Ceramic Composites, and Vulcan Shield Group.
The RATH Group, headquartered in Vienna, Austria, is known for its extensive experience in refractory materials. The company has recently completed the development of continuous oxide ceramic fibres and is due to ramp up production over the coming years. This move is set to diversify the current market, which has been largely dominated by 3M with its Nextel range of fibres. RATH's new fibres aim to match or exceed the performance characteristics of the Nextel offerings, particularly in terms of high temperature stability and creep resistance. RATH is producing alumina-based fibres (Al2O3) and mullite fibres, a blend of alumina and silica (SiO2). RATH’s focus on continuous fibre technology marks a significant step forward from the more commonly produced short fibres, offering potential for more robust and versatile CMCs.
Saint-Gobain Advanced Ceramic Composites, based France, represents a transformation from its quartz fibre production to a broader advanced ceramic composite focus. This transition is part of its strategy to break into the alumina fibre market, currently expanding its product base to include continuous alumina and mullite ceramic fibres. These fibres are designed to offer superior thermo-mechanical resistance and stability up to 1200°C, pushing the boundaries of current oxide fibre capabilities. Saint-Gobain's innovation extends to its cooperative development strategies, such as its partnership with the Denkendorf Institute for Textile and Fiber Research (DITF) in Germany. This collaboration has culminated in the development of fibres that not only compete with but also aim to surpass the performance of established products like 3M’s Nextel series. Saint-Gobain’s new fibres enhance high temperature applications by providing better dielectric properties and mechanical strength, making them suitable for aerospace and defence applications that demand lightweight yet durable materials.
Vulcan Shield Group’s (VSG) 2024 Product Catalogue introduces an array of alumina continuous fibres, highlighting their capability to operate under extreme temperatures (1200 - 1300°C) and their significant oxidation and corrosion resistance. VSG's fibres are differentiated by their alumina content, with variants ranging from 72% to 99% alumina. VSG’s alumina fibres, particularly the M-99 series with over 99% alumina content, may offer a good balance of interfacial control, high-temperature strength, and corrosion resistance. This makes them ideally suited for both metal and ceramic matrix composites and other high temperature applications. VSG’s focus on customisability and scalability in production reflects a keen responsiveness to market needs, positioning their fibres as versatile and competitive options in the global CMC market.
“The development of new ceramic fibres by RATH, Saint-Gobain, and Vulcan Shield Group signifies a significant shift in the Oxide CMC landscape. These advancements not only enhance the performance parameters of ceramic fibres but also increase competition in the market, expanding their applicability across many more applications. Historically dominated by 3M, whose Nextel fibres have set industry standards for years, the market is poised for transformation as these new entrants introduce potentially competitive alternatives. This increase in competition is likely to exert downward pressure on prices, making high performance alumina-based fibres more accessible and affordable. The broadened availability and potentially lower cost of oxide fibres could accelerate adoption and innovation, expanding the use of CMCs in both traditional and new applications.”
Dr. Richard Grainger, CTO of HTMS.
HTMS Capability
High Temperature Material Systems Limited (HTMS), established in 2021 by Dr. Danilo Di Salvo and Dr. Richard Grainger, is at the forefront of developing innovative CMCs for cost sensitive sectors. Leveraging advanced research and development capabilities, HTMS is committed to pioneering new matrix chemistries that enhance performance, durability, and functionality of CMCs. Their unique proprietary matrix system is distinguished by its low temperature processing capabilities, which not only reduce CO2 emissions by approximately 50% compared to traditional oxide CMC systems but also prevent damage to sensitive fibres that cannot withstand high temperatures.
This innovative approach allows HTMS to utilise a wide range of fibres previously unsuitable for CMCs due to processing constraints. By incorporating such fibres, HTMS can offer customised solutions tailored to the specific needs of their customers while circumventing the need for more costly, conventional fibres. For instance, basalt fibres, which would typically be damaged in high temperature sintering processes, are used effectively by HTMS to create cost efficient fire, smoke, and toxicity (FST) shields. HTMS's method has demonstrated that these basalt fibre based composites show minimal degradation even when tested at temperatures as high as 800°C. The affordability of basalt fibres, in comparison to traditional oxide fibres, presents a significant cost advantage, enabling HTMS to deliver high performing, lower cost CMCs to their customers.
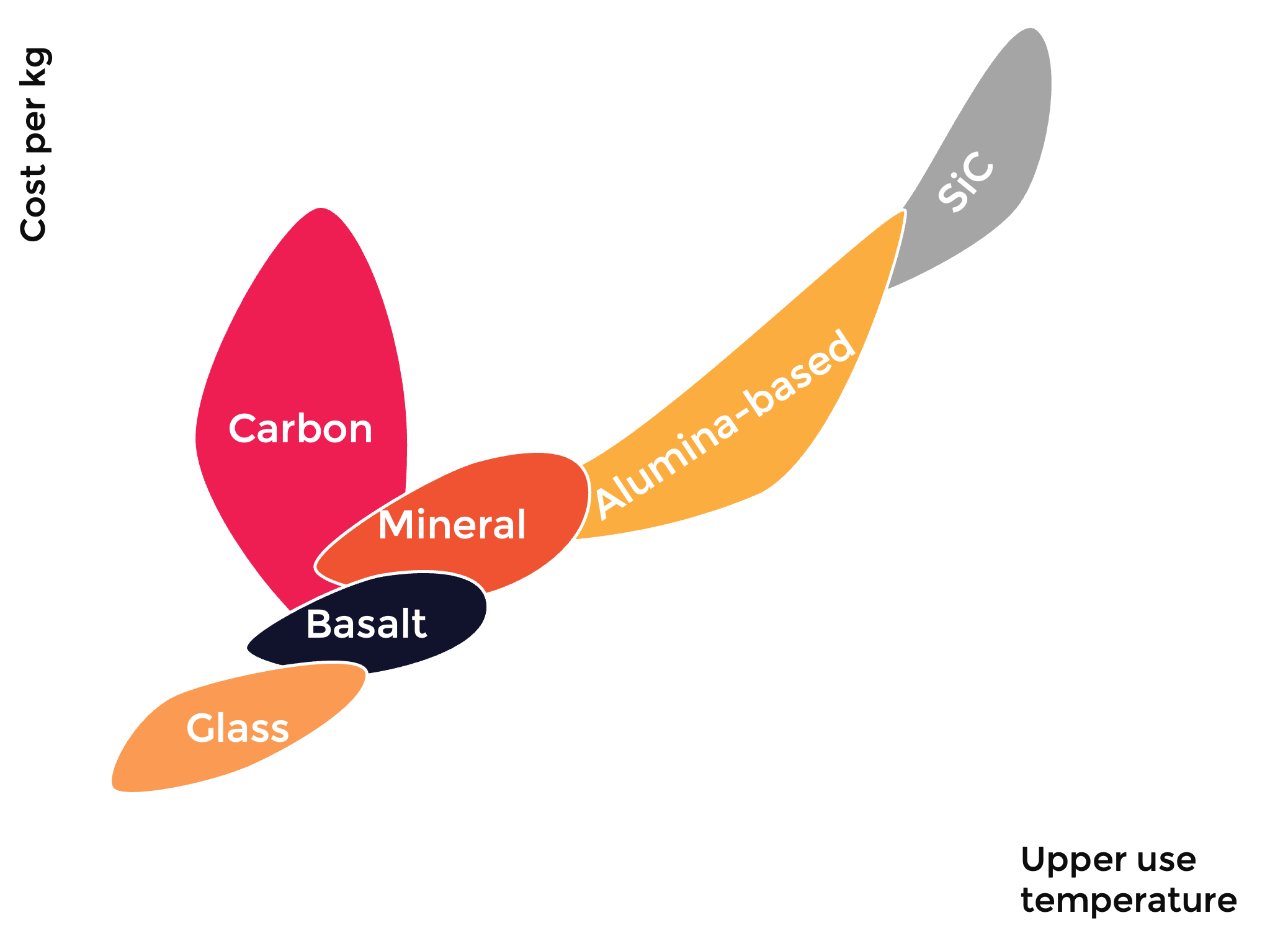
Furthermore, HTMS has successfully produced CMCs utilising a variety of other fibres, including glass, carbon, and mineral fibres, all of which offer customisable properties to meet diverse application requirements. This flexibility in fibre selection underscores HTMS’s ability to innovate within the CMC industry, providing versatile, high quality solutions that address both performance and budgetary constraints of their clients.
Summary
In conclusion, the development of new ceramic fibres by RATH, Saint-Gobain, and Vulcan Shield Group marks a significant transformation in the oxide CMC landscape, enhancing the performance parameters of ceramic fibres and broadening their applicability across various industries. Traditionally dominated by 3M, whose Nextel fibres have set industry standards for years, the market is poised for a shift as these new players introduce competitive alternatives. HTMS also emerges as a key innovator, leveraging unique low-temperature processing techniques to utilise a wider range of fibres and provide cost-effective, tailored solutions. This burgeoning competition is expected to drive down prices, making high performance ceramic composites more accessible and cost effective. As these new products enter the market, they promise to elevate the material standards for CMCs, fostering innovation in sectors that rely on high durability and exceptional thermal resistance, and potentially disrupting 3M's long standing market dominance.