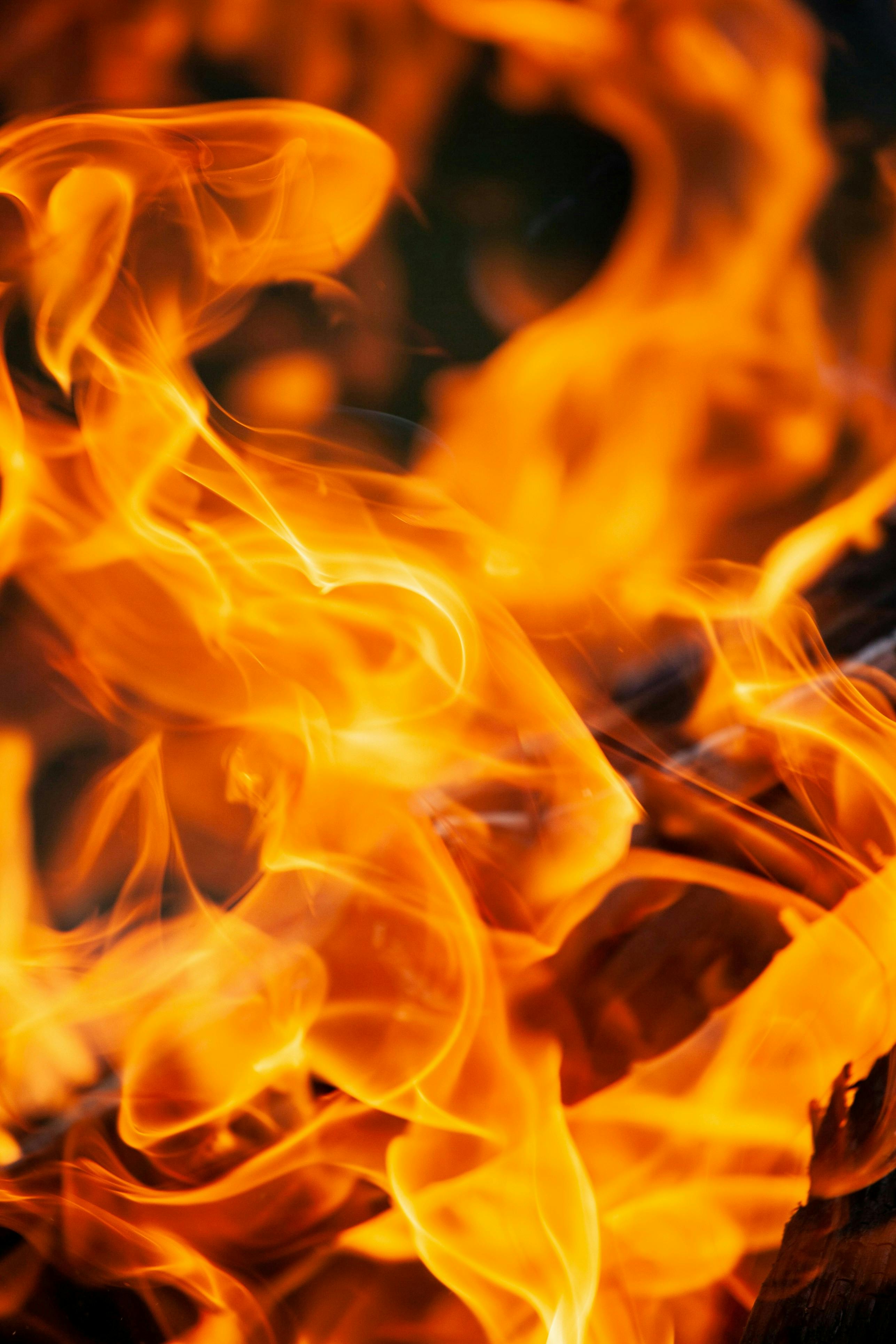
Introduction
Lithium batteries are becoming ubiquitous in our daily lives. From our phones and laptops, scooters, cars and planes, to powering the very homes we live in, high-density electrical storage is dominated by Lithium-based chemistries. While the perceived risk from these devices is generally low, there is increasingly unease about the safety of some of these systems where performance is being pushed to the limit, and the capability of the enclosures has to keep up. While rare, the extreme heat caused by battery fires can cause serious risk to human life if the materials are not developed which can withstand and contain failures to allow emergency procedures to take over.
Evolution of battery systems
Transport industries have long been exploring energy storage systems to provide power and backup support to critical equipment. From the era of Lead-Acid batteries to the evolution of Nickel-Cadmium batteries, there has been a continuous pursuit of battery systems with higher power and energy density to meet the industry's evolving needs.
A step change came in the form of Lithium-Ion battery chemistry, commercially introduced by Sony in 1991. This chemistry promised a 4 to 5 times improvement in energy/power density, with approximately half the size and weight compared to alternatives. However, at that time it was already known that there was a potential risk in using these high-energy systems. The recall of MOLI’s Li-metal rechargeable cells some years before the release of rechargeable metal anode-based lithium batteries was a reminder of these risks. Early Li-Ion battery systems experienced highly publicized commercial failures, such as the Samsung Note 7 battery fiasco in 2016, caused by manufacturing defects lead to significant public scepticism. The aerospace industry has also faced similar challenges, with the FAA reporting 470 aviation-related incidents involving lithium batteries from March 3, 2006, to December 28, 2023. Notable aviation incidents, like the Ethiopian Airways 787 fire at Heathrow Airport in 2013 and the Japan Airlines 787 at Boston Airport the same year, heightened consumer awareness and prompted safety regulations to better understand the performance and limitations of Li-Ion cells and batteries.
These efforts have led to the introduction of new approaches to mitigate the thermal reactivity of Li-Ion products. Furthermore, military and regulatory agencies have implemented new Minimum Operating Performance Standards (MOPS), such as RTCA DO-311A and MIL-PRF-29595A, offering clear guidance on the development, testing, and certification requirements for Lithium-Ion battery systems.
In the search for lower costs and higher energy densities the materials and manufacturing methods become more critical. With a separator thickness of only 20–25 µm, any small intrusion of metallic dust or other particles can have devastating consequences. Whereas a nail penetration test could be tolerated on the older 18650 cell with a capacity of 1.35 Ah, today's high-density cells with >2.4 Ah would react with fire and material release when performing the same test. Lithium-ion batteries are nearing their theoretical energy density limit and battery manufacturers are stepping up their efforts to focus on improving manufacturing methods and increasing safety.
Risks posed by Lithium batteries
There are a number of risks posed by these higher energy-dense batteries which need to be carefully considered.
Overcharging poses a significant risk to rechargeable lithium batteries, distinct from nickel-cadmium or lead-acid batteries. This risk may result in thermal runaway, where overcharging leads to an uncontrolled increase in temperature and pressure. Additionally, overcharging can impact internal cell components, emphasizing the importance of considering battery capacity, not just size, due to the higher amount of electrolyte and energy involved.
Over-discharging is another concern, particularly for certain types of batteries discharged beyond a specific voltage, typically 2.4 volts. This can lead to corrosion of electrodes within the cells. Recharging damaged rechargeable lithium batteries, following over-discharging, may trigger an uncontrollable exothermic reaction. Corroded electrodes can themselves become a source of short circuits (see image), with a dendrite of corrosion growing from one electrode towards the other, resulting in an internal short.
Internal short circuits present a risk attributed to various factors, including manufacturing defects, impurities, and foreign object deposits. The occurrence of an internal short circuit may lead to an uncontrolled increase in temperature and pressure, ultimately resulting in thermal runaway.
Furthermore, the possibility of reverse voltage in non-rechargeable lithium batteries, especially those with more than one cell, is an important concern. This can even lead to a thermal runaway event, posing additional risks associated with uncontrolled temperature and pressure increase.
Although there many risks associated with lithium batteries, as discussed, due to their clear advantages there is a need to alleviate these so as to maintain or even increase performance. There are many methods to reducing these risks, including by software (monitoring), electronic hardware (BMSs, temp sensors, fuses), structural design (keep batteries away from key systems), early warning systems (fire/smoke detectors), and by using materials with greater fire resistance.
In the current article there is a focus on the materials used for enclosures, what makes a safe enclosure, and how we test for suitable materials for the job.
Measurement of fire-resistant materials
While fire resistance is an extremely complex area, it can be broken down into a number of individual measures. This is by no means an exhaustive list, for further information, please consult the further reading found in the Resources at the end of this article.
Ignition
Ignition is the start of a fire, and thus the ‘ignitability’ of a material is the general term given to a materials ability to support combustion when exposed to a naked flame under normal atmospheric conditions. This definition is contested, however, with technical and general definitions overlapping and, in some cases, contradicting. The BS 476 suite of standards laid out by the British Standards Institute dictates fire tests for materials used in the construction industry, but due to their pre-existing standards have become common throughout engineering, and contains a number of tests for determining ignitability, eg BS 476-13:1987. A materials ability to ignite under these condition is a combination of its fundamental properties, and as such some materials may not be ignitable but still be able to support fire in later stages, when conditions such as temperature and reactant availability have changed. Materials which are unable to support combustion under any circumstances are considered to be non-combustible.
Combustibility
The term ‘combustibility’ refers to the tendency of a substance to burn as a result of fire or chemical reaction. It is can be expressed as a property that is a measure of how easily a substance will ignite or burn, an important consideration when materials are being used or stored for construction purposes. The term ‘flammable’ may be used to describe substances that ignite more easily, whilst substances that are harder to ignite or that burn less intensely may be referred to as combustible. Less combustible materials may be described as 'materials of limited combustibility'. At the extreme end of the scale is ‘non-combustible materials’ which do not support fire at all.
Some common definitions of ‘non-combustible materials’:
- Any material which when tested to BS 476-11:1982 (2007) does not flame nor cause any rise in temperature on either the centre (specimen) or furnace thermocouples.
- Products classified as non-combustible in tests following the procedures in BS 476-4:1970 (2007).
- Any material classified as class A1 in accordance with BS EN 13501-1:2002 Fire classification of construction products and building elements. Classification using data from reaction to fire tests.
- ISO 1182:2020 which defines a test method for determining non-combustibility performance, under specific conditions.
As an aside, the construction industry has also had some issues with fire-proof materials in recent years. Following the Grenfell Tower Fire, a decision was taken to ban combustible materials in the cladding for buildings over 18m in height. The issue was raised again in November 2019 following a fire at The Cube in Bolton. In this case HPL cladding was used, and the building was less than 18m in height, resulting in calls for the ban on combustible cladding materials to be extended.
Heat Release Rate
There are a number of other measures of materials contribution to fire, or risk of fire, which are used in general across all industries.
The heat release rate has been considered by some in the academic community to be the single most important variable in determining the fire hazard posed by different materials. It is a measure of the amount of energy lost per second (I.E. power), normalised to surface area of the material, therefore measured in kW / m2. In polymer-matrix composite materials, one of the main contributors to the HRR is from hydrocarbon volatiles being released from the burning surfaces, which migrate from the decomposing matrix into the flame where they contribute their heat of combustion via oxidation. The heat release rate at different heat fluxes can be measured with a bench-scale calorimeter, which rely on the principle of oxygen consumption, i.e., materials undergoing complete combustion release a constant amount of heat per unit mass of oxygen consumed. Despite the risks to life posed by ignitability as well as smoke and toxicity, HRR is often regarded to the best predictor of overall risk as it is a global measure of a materials contribution to combustion progress.
Smoke and Toxicity
Another way of measuring risk of fire is by analysing smoke and toxicity of fire-released gasses. One of the most immediate dangers from combusting materials is smoke and toxic gases released from the flames, and outgassing of hazardous products from the surfaces of materials undergoing thermal breakdown. It is commonly understood that a greater risk is posed from the gaseous toxic by-products of a fire than from the flames themselves.
Smoke and toxic gasses can be quantified in cone calorimeter tests by measuring the intensity of light that is transmitted through the smoke in the exhaust duct. Alternatively, the amount of combustion products given off by a sample is related to the mass loss during the combustion process. Specimens in the test are burned above a weighing device while being subjected to an external irradiance within the range of 0 to 100 kW/m2 to measure a ‘mass loss rate’.
While these general measures give an indication of the amount of smoke is given off during certain combustion conditions, whether in volume or visual density, it does not indicate the level of risk the smoke directly presents to humans breathing it. For this to be measured, the smoke must be analysed to determine the specific chemical components and compare this to the chemicals known toxicity to humans.
Tests have been conducted specifically investigating the chemical composition of gasses released during lithium battery fires. Gas components are mainly carbon monoxide, carbon dioxide, methane, ethane, ethene, and H2. Within these emitted gases can also be traces of hydrogen fluoride, phosphine, formaldehyde, acetaldehyde, propionaldehyde, butyraldehyde, valeraldehyde, and 1,3,5-trifluorobenzene. The source for fluorine components in released gases is LiPF6 which thermally decomposes at about 90°C to lithium fluoride (LiF) and phosphor(V)-fluoride (PF5) which reacts in the presence of traces of water to HF and phosphorus oxide fluoride (POF3), both compounds are toxic.
Designing enclosures for aerospace
In order to design an enclosure for fire and hazard containment for a lithium or other high power battery system a number of steps would need to be followed.
Firstly, the fire threat needs to be precisely defined. This entails the product supplier, responsible for providing the item serving as the fire source, conducting an analysis and outlining the specific nature of the fire risk.
The definition of the fire resistance of the enclosure should align with both cabin safety and structural requirements, adhering to the relevant Cabin Safety Regulations (CSs). Ensuring compliance with these regulations is crucial in determining the enclosure's suitability for the intended purpose.
From a structural perspective, especially at the aircraft level, considerations of strength and stiffness become paramount. Addressing these factors is essential in accordance with damage tolerance considerations, as outlined in AMC 20-29 Categories of damage.
A critical reference point in this assessment is the glass transition temperature, denoted as Tg. It is recommended to maintain a minimum margin of 50ºF between the Maximum Operating Temperature (MOT) and Tg for the composite material. Additionally, a 30ºF margin is advised concerning any adhesives used in the construction.
This structural evaluation primarily applies to the area surrounding the composite box. The box, when exposed to the identified fire threat, must effectively contain the fire to prevent the surrounding load-bearing structure from surpassing the Maximum Operating Temperatures (MOTs) determined by the airframe designer, influenced by factors such as material selection.
There are further considerations in the cabin safety requirements including addressing toxicity and smoke density, as mentioned earlier, to ensure the overall safety and well-being of occupants in the event of a fire.
Summary
Materials for future energy systems will require higher fire performance to meet increasing safety demands. While there is a clear advantage for safety using batteries over conventional fuels, as there is no explosive material on board, it must be borne in mind that other risks arise with the introduction of an electric power source. These new risks are less familiar to users and emergency responders. The need to withstand extreme temperature environments, not react with by-products of combustion and also maintain structural integrity to prevent further collapse or contact with other systems is a challenge for materials which are under constant scrutiny from design teams looking for lighter and cheaper alternatives.
While polymer composite materials have been the go-to source for answers to increase specific strength and damage tolerance to lighten aircraft, they fall short in applications which need to resist strong thermal, electrical or chemical attack. An increasingly popular class of materials replaces the polymer matrix with ceramic, creating a completely non-combustible material which can also maintain structural integrity even in the most extreme temperature scenarios.