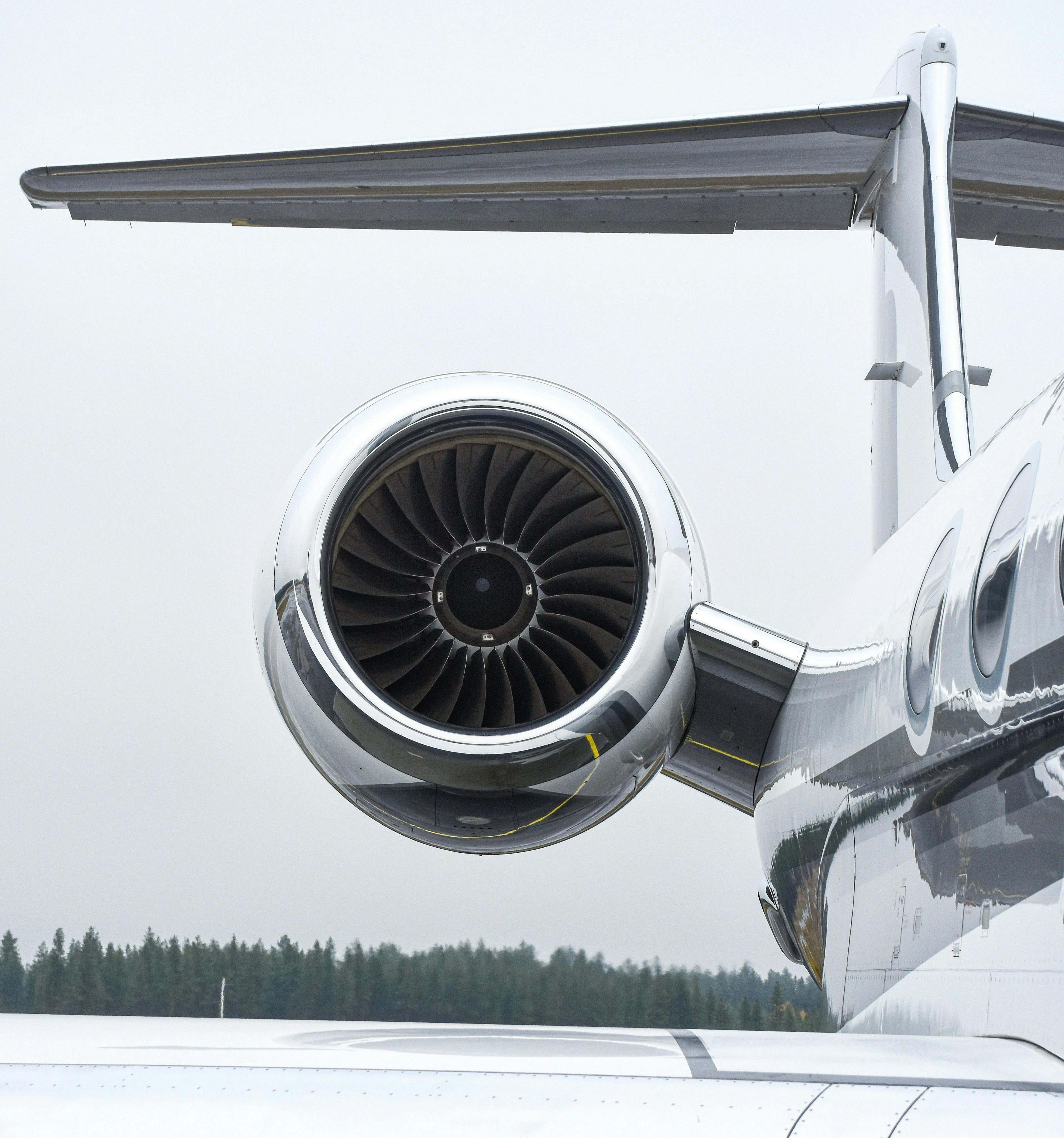
Introduction
In the realm of materials science, the quest for materials capable of withstanding extreme conditions while maintaining their integrity and performance has led to significant innovations. Among these, Oxide/Oxide Ceramic Matrix Composites (CMCs) represent a pivotal advancement, offering a blend of properties that traditional metallic materials cannot match. These composites, developed to leverage the high temperature capabilities of ceramics without their inherent brittleness, have emerged as a key solution for applications demanding durability and resistance to thermal and oxidative stress. The inception of Oxide/Oxide CMCs marked a significant leap in overcoming the limitations of conventional composites. Designed with a focus on high temperature performance, these materials combine oxide ceramic matrices with reinforcing oxide fibres, yielding composites that excel in environments where metal alloys and non-oxide ceramics can weaken. The intrinsic resistance to oxidation and thermal degradation of Oxide/Oxide CMCs has rendered them an interesting solution in sectors such as aerospace, defence, and energy—industries where materials are routinely subjected to harsh thermal environments and oxidative atmospheres.
Innovations in fibre technology, matrix compositions, and processing methods have enhanced the mechanical properties and durability of Oxide/Oxide CMCs, making them more cost-effective and environmentally sustainable than their predecessors. As we delve into the complexities and contributions of Oxide/Oxide CMCs, we uncover their transformative potential in shaping future material science and engineering, underscoring their role in advancing technological frontiers and meeting the challenges of modern engineering applications.
Historical Development and Material Properties
The historical development of CMCs, particularly Oxide/Oxide CMCs, marks a significant evolution in materials engineering, aiming to meet the demands of high temperature applications where conventional materials fall short. Initially, CMCs were developed to leverage the high-temperature capabilities of ceramics while mitigating their inherent brittleness by incorporating reinforcing fibres, thereby enhancing their toughness and durability. Oxide/Oxide CMCs emerged as a category within this broader field, designed to offer superior resistance to oxidation and thermal degradation compared to non-oxide counterparts like Silicon Carbide (SiC)/SiC composites. This intrinsic resistance to high temperature oxidation is pivotal for applications in the aerospace and energy sectors, where materials are regularly exposed to extreme thermal environments and oxidative atmospheres.
The material properties of Ox/Ox CMCs are defined by their unique composition: an oxide ceramic matrix reinforced with oxide ceramic fibres. This combination not only provides excellent thermal and oxidative stability but also maintains mechanical integrity at temperatures where metals and non-oxide ceramics would fail. The advancement in fibre technology, particularly the development of alumina-based fibres like Nextel 610 and 720, has played a crucial role in enhancing the strength and temperature capability of Ox/Ox CMCs, making them viable for more demanding applications. Moreover, the porosity of the matrix is carefully engineered to optimise the composite's mechanical properties, including its fracture toughness and resistance to thermal shock. These material characteristics are critical for the performance and reliability of Ox/Ox CMCs in service, allowing them to withstand not just high temperatures but also the mechanical stresses and environmental conditions typical of their applications.
The technological advancements in the manufacturing of Oxide/Oxide CMCs have been pivotal in addressing their historical limitations and enhancing their applicability across various high-temperature environments. Innovations have focused on refining fibre production, matrix formulations, and sintering processes. The development of high-quality oxide fibres has been crucial, with specific advancements in the spinning and heat treatment processes to achieve fibres that offer improved strength and durability at high temperature. In matrix technology, the introduction of novel slurry impregnation techniques and sol-gel processes has enabled the creation of denser, more uniform matrices that can distribute loads more effectively under multi-axial loading.
Sintering techniques have also seen significant improvements. Lower temperature sintering processes have been developed to minimise fibre damage during composite fabrication, preserving the integrity and mechanical properties of the fibres within the matrix. This progress in manufacturing technology not only makes Ox/Ox CMCs more cost-effective but also expands their potential as a sustainable alternative to other high temperature materials.
Comparing Oxide/Oxide CMCs with their Non-Oxide counterparts reveals a landscape marked by distinctive advantages and trade-offs, tailored to specific application requirements. Oxide CMCs stand out for their exceptional oxidation resistance and stability in high-temperature environments. Non-Oxide CMCs, such as those reinforced with Silicon Carbide (SiC) fibres, offer superior mechanical properties at extreme temperatures, including higher strength and stiffness. However, their susceptibility to oxidation at elevated temperatures limits their performance over time, necessitating protective coatings that add complexity and cost to their application.
The advancements in Oxide/Oxide CMCs, particularly in fibre technology and matrix compositions, have significantly bridged the performance gap between Oxide and Non-Oxide CMCs. Innovations in manufacturing processes have also played a crucial role, enhancing the mechanical properties and durability of Oxide/Oxide CMCs while maintaining their cost-effectiveness and simplifying their integration into existing systems. Oxide/Oxide CMCs present a more cost-effective solution over the long term, considering their lower maintenance requirements and longer service life in oxidative environments. This economic advantage, combined with ongoing technological advancements, positions Oxide/Oxide CMCs as a compelling alternative for a wide range of high temperature applications, challenging the dominance of Non-Oxide CMCs and traditional high-temperature metallics.
Strategic Importance Across Industries
The strategic importance of Oxide/Oxide CMCs spans multiple industries, revolutionising how critical components are designed and implemented for enhanced performance and efficiency. In the aerospace sector, these materials are growing in popularity for combustor and turbine statics, where their high-temperature resistance and oxidation stability significantly improve engine efficiency and reduce maintenance requirements. Similarly, in the energy industry, their ability to withstand corrosive and high-temperature environments makes them ideal for components in power generation systems, contributing to more sustainable and efficient energy production. This cross-sectoral application underscores their transformative potential.
HTMS has played a pivotal role in the evolution and application of Oxide-based CMCs, marking a significant stride in the field of advanced materials. Their contributions have been instrumental in addressing some of the critical challenges that have historically limited the wider adoption of these composites. By pioneering innovative matrix chemistries and processing techniques, HTMS has enhanced the mechanical properties and thermal stability of Oxide/Oxide CMCs, making them more viable for high-temperature applications. One of the key advancements brought about by HTMS is the development of novel matrix materials that can be sintered at lower temperatures. This breakthrough reduces the risk of damaging the reinforcing fibres during the manufacturing process, thereby preserving the composite's integrity and performance capabilities. Such innovations not only improve the quality of the final product but also contribute to reducing production costs, making Oxide/Oxide CMCs a more attractive option for industries reliant on materials that can withstand extreme conditions.
The landscape of advanced materials engineering is witnessing a transformative phase with the maturation of Oxide/Oxide CMCs. These materials face a trifecta of challenges that delineate the current frontier of research and application. Primarily, the quest for enhanced material properties — strength, durability, and temperature resistance — remains at the forefront. This pursuit is not merely academic; it directly impacts the viability of Oxide/Oxide CMCs in extreme environments, where traditional materials succumb to the rigors of high temperatures and corrosive atmospheres. Furthermore, the scalability of manufacturing processes for Oxide/Oxide CMCs presents a significant hurdle. The specialised techniques required to produce these composites demands a level of precision and control that complicates large-scale production. Achieving cost-effectiveness, a critical factor for widespread adoption, hinges on innovating manufacturing technologies that can maintain the exquisite balance between quality and throughput. Moreover, the integration of Oxide/Oxide CMCs into existing systems and materials frameworks underscores a broader challenge of compatibility and adaptability. The development of effective joining techniques, alongside ensuring material compatibility, is essential for the seamless incorporation of these composites into complex assemblies and applications.
Concurrently, advancements in manufacturing technology are set to revolutionise the production landscape for these materials. The advent of additive manufacturing, automated fibre placement, and rapid sintering processes offers a glimpse into a future where Oxide/Oxide CMCs can be produced with unprecedented efficiency and complexity. This evolution in manufacturing is not just about scaling up; it’s about unlocking new geometries, functionalities, and applications that were previously unattainable. As we look to the future, the broader industrial adoption of Oxide/Oxide CMCs seems not just feasible but inevitable. The expanding role of these composites in aerospace, defence, green transport, energy, fire protection and potentially new sectors speaks to their strategic importance in the next wave of technological advancements. In essence, the journey of Oxide/Oxide CMCs is emblematic of the broader trajectory of materials science — a field defined by its challenges but driven by the unyielding pursuit of solutions. As these materials edge closer to realising their full potential, they underscore a commitment to not just meeting the demands of modern engineering challenges but advancing the frontiers of sustainability and efficiency in the process.
Conclusions
The journey of Oxide/Oxide CMCs from their inception to their current standing in the materials engineering landscape encapsulates a narrative of innovation and strategic importance across multiple industries. These composites, heralded for their unparalleled resistance to high temperatures and oxidation, have carved a niche for themselves in critical applications where traditional materials fall short. The evolution of Oxide/Oxide CMCs, underscored by significant advancements in material properties and manufacturing processes, reflects a concerted effort to address the stringent demands of high-temperature environments in aerospace, defence, and energy sectors.
The strategic adoption of these materials in gas turbines and power generation components has not only enhanced performance and efficiency but also underscored the transformative potential of Oxide/Oxide CMCs in driving advancements in material science and engineering. The role of entities like HTMS in pioneering innovations in matrix chemistries and processing techniques has been instrumental in overcoming historical limitations, marking a significant stride in the field of advanced materials. These contributions have optimised the mechanical properties and thermal stability of Oxide/Oxide CMCs, making them more viable and attractive for high-temperature applications.
However, the path forward for Oxide/Oxide CMCs is not devoid of challenges. The quest for enhanced material properties, scalability of manufacturing processes, and integration with existing systems presents hurdles that demand innovative solutions. The future of Oxide/Oxide CMCs lies in the promise of material science breakthroughs and advanced manufacturing technologies that aim to redefine performance benchmarks and expand their application scope. The potential for broader industrial adoption and the role of collaborative ecosystems in fostering innovation highlight the ongoing commitment to not just meet but exceed the demands of modern engineering challenges. This narrative underscores a broader trajectory towards sustainability and efficiency, positioning Oxide/Oxide CMCs at the forefront of materials science, ready to meet the evolving demands of the future.